What is valve?
Valve is a fluid delivery system in the control components, used to open and close the pipeline, control the flow direction, regulation and control of the parameters of the transport medium (such as temperature, pressure and flow). Valves can be manually operated, automated, or even remotely controlled. Valve has a cut-off, regulation, infusion, to prevent reverse flow, stable pressure, shunt or overflow pressure relief and other functions, widely used in the control of air, water, steam, a variety of corrosive media, slurry, oil, liquid metals and radioactive media and other types of fluid flow.In summary, valves are versatile tools that enable the safe and efficient management of fluid flow in various engineering systems.Common in our daily life are gate valves, butterfly valves, globe valves, ball valves and check valves
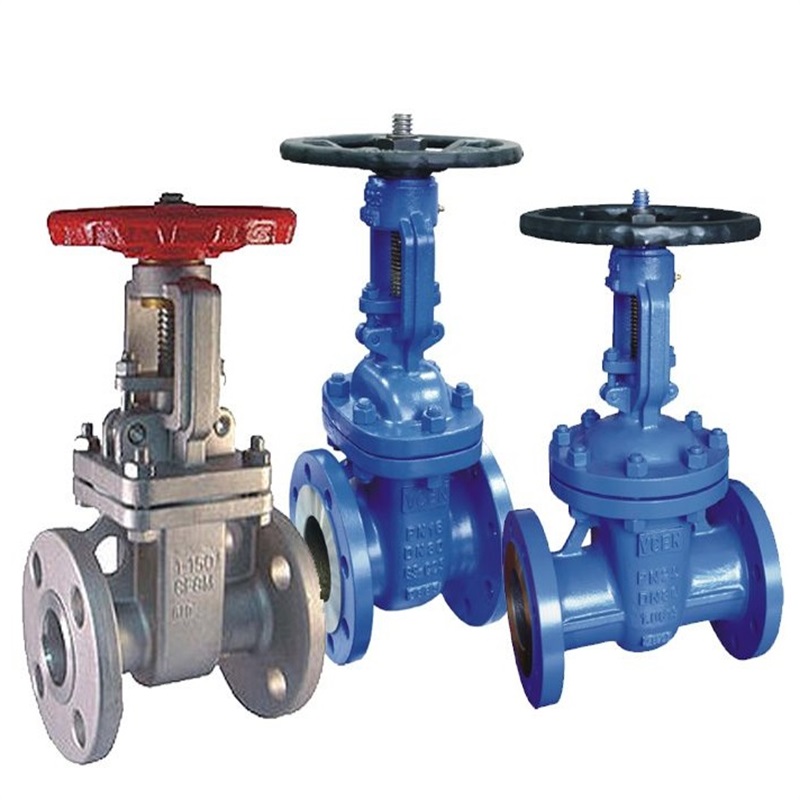
Classification of valves
1. Butterfly valve
Butterfly valve is a compact structure, open and close the valve quickly, the valve flap is disc-shaped, rotating around the valve axis to control the fluid on and off. Butterfly valve is small in size and light in weight, suitable for large diameter pipeline and low pressure system, easy to operate, with good flow regulation.Suitable for large-diameter pipelines and occasions that require rapid opening and closing, Its sealing performance is good, widely used in water, air, oil and other media control.
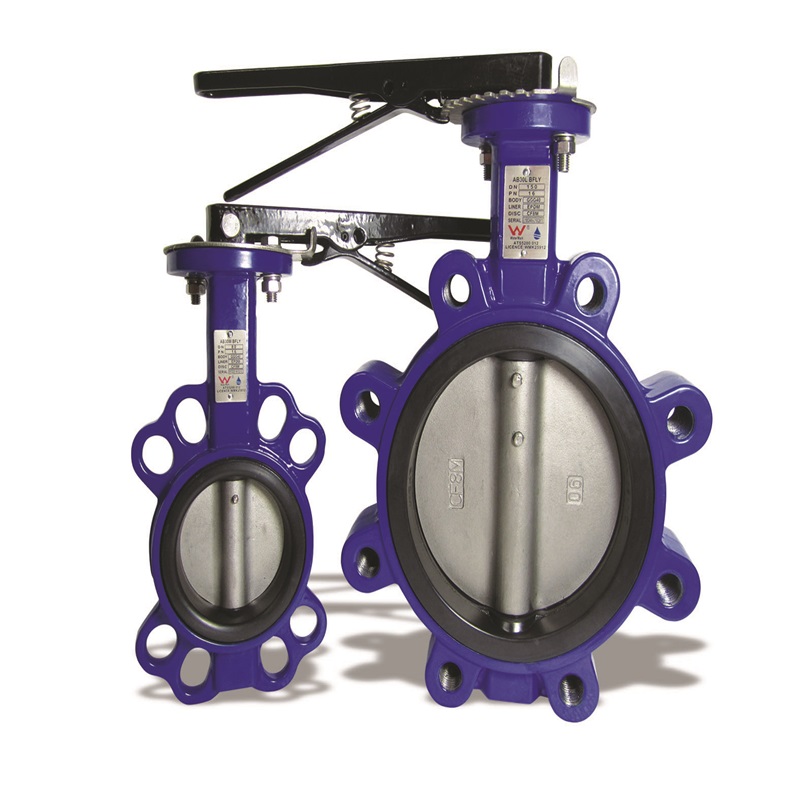
- 2.Gate Valve
Gate valve is a kind of valve through the gate lift to control the fluid on and off, with small fluid resistance, good sealing performance. Mainly used for fully opening or fully closing the medium in the pipeline,The gate valve is sealed by the contact between the valve seat and the gate. Gate valve structure is complex but stable and reliable, suitable for high-pressure, large-diameter pipelines, can be fully open or fully closed, good regulation performance, widely used in petroleum, chemical,natural gas, water conservancy and other fields.
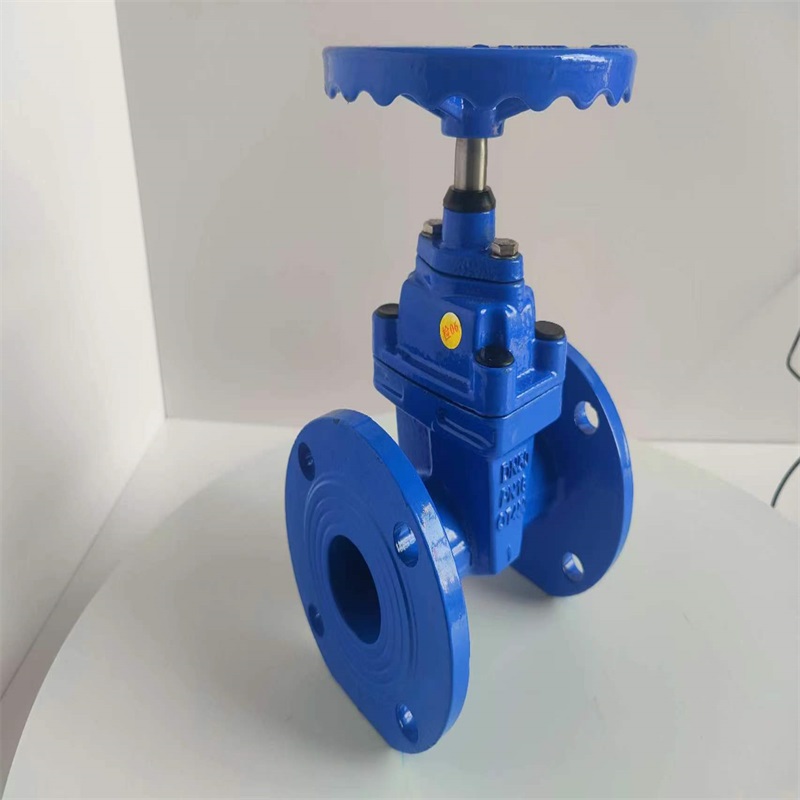
3.Globe Valve:
Opening and closing are achieved by moving the valve disc along the axis of the valve seat. It is mainly used to cut off the fluid and can also be used to adjust the flow .Suitable for occasions with low requirements for adjustment performance, such as water supply and drainage systems, thermal systems, etc.
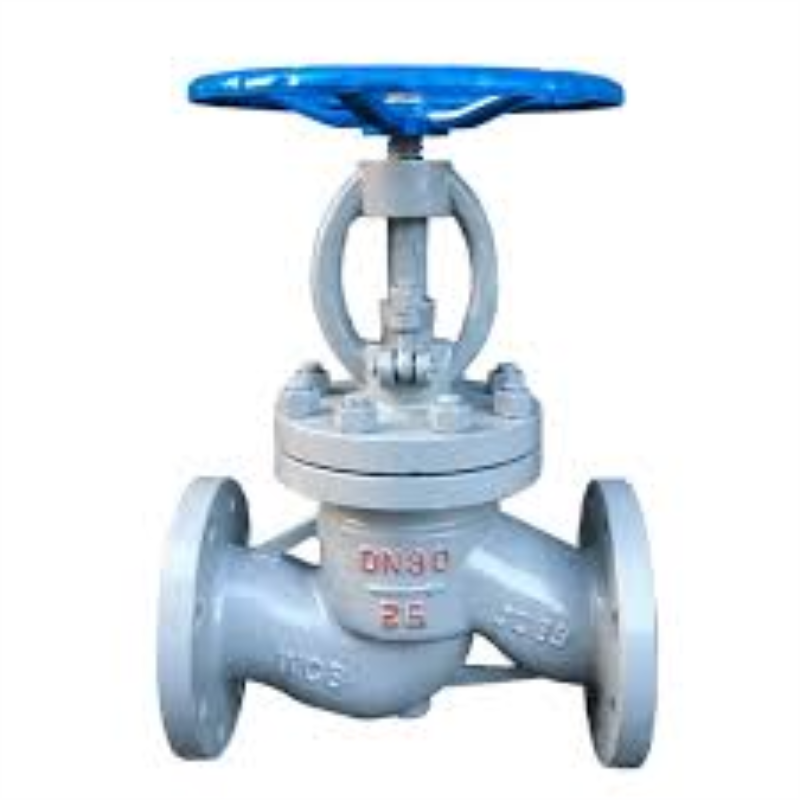
4.Ball Valve:
The function of the ball valve is to control the opening and closing of the valve by rotating the ball, with the advantages of small fluid resistance and rapid opening and closing. Widely used in the oil, natural gas, chemical, food and other industries as valves to cut off, distribute and change the flow direction of the medium.
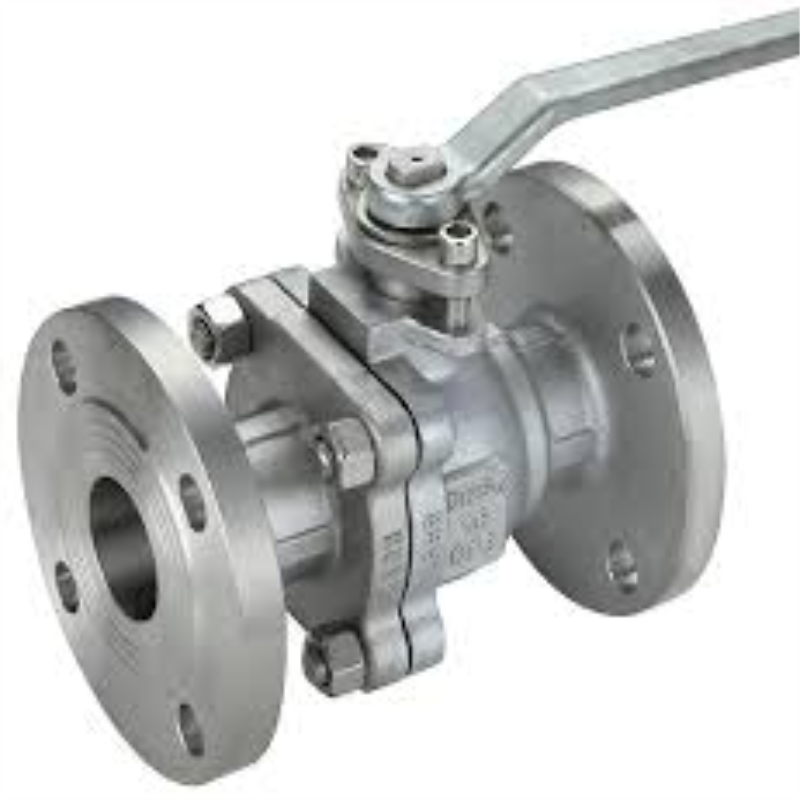
5.Check Valve:
Check valve is a kind of valve that can automatically prevent the medium from flowing backwards, its design is exquisite, simple structure. In the positive flow of fluid, the check valve opens to ensure the smooth passage of the medium; once the fluid flows in the opposite direction, the check valve closes immediately, effectively preventing the medium from flowing backward,Installed at the outlet of the pump or other pipelines where the medium to protect the pipeline and equipment safety. Check valves are widely used in various fluid control systems.
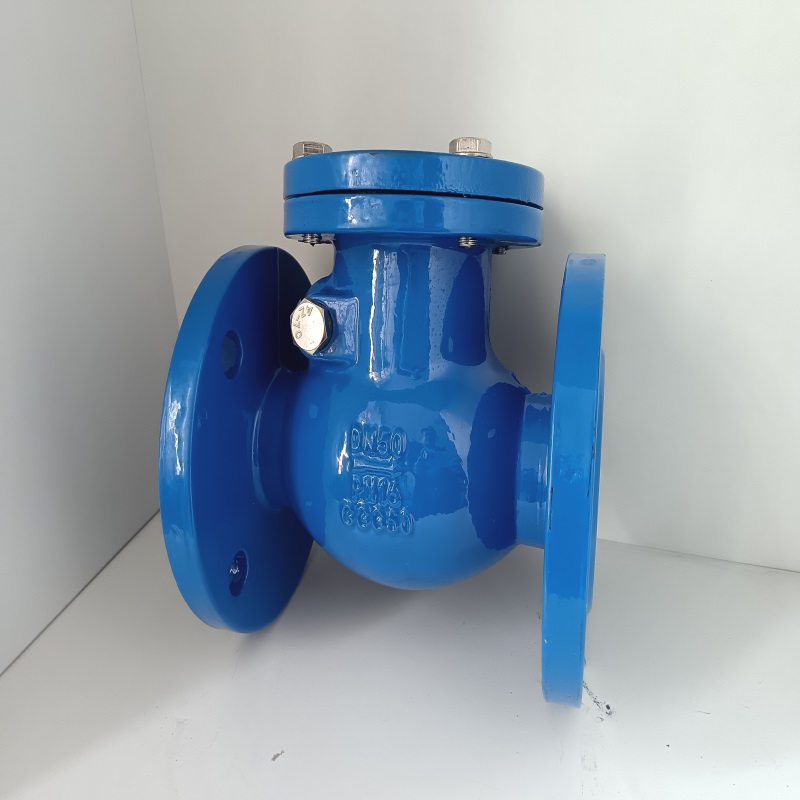
6. Water control valve
Water control valve is a vital component in the water conservancy system, through the precise adjustment of water pressure, flow and other parameters to ensure the stable operation of water conservancy facilities. It has excellent sealing performance, corrosion resistance and durability, easy to operate and maintain. Water conservancy control valves are widely used in irrigation, water supply and drainage, water treatment and other fields, is to ensure the efficient operation of water conservancy system of key equipment.
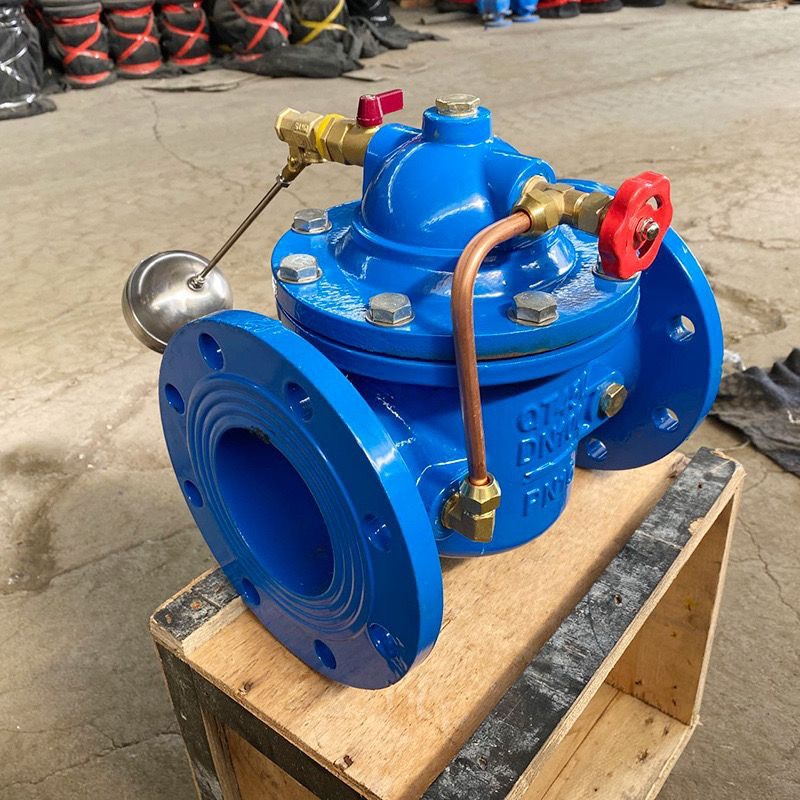
The production process of valves:
① Design: According to the use requirements and working environment, design the valve structure, material and size and other parameters. The design process needs to consider the function of the valve, sealing performance, pressure resistance and other factors.
② Material selection: according to the design requirements, select the appropriate material for manufacturing. Common valve materials include cast iron, cast steel, stainless steel, copper alloy and so on.
③ Material processing: according to the design drawings, the selected material will be cut, forging, casting and other machining processes, manufacturing the various parts of the valve.
④ Assembly: the processed parts for assembly, including the installation of the valve body, valve cover, valve stem, valve seat, seals and so on. The assembly process needs to pay attention to the matching accuracy of the parts and the installation order.
⑤ Detection: carry out various tests on the assembled valve, including appearance check, size test, sealing performance test. Ensure that the quality of the valve meets the design requirements.
⑥ Surface treatment: according to the needs of the valve surface treatment, such as spraying anti-corrosion paint, galvanised, etc., to improve the corrosion resistance of the valve.
⑦ Packaging and shipment: Pack the manufactured valves and ship them out for sale or transport to the place of use.
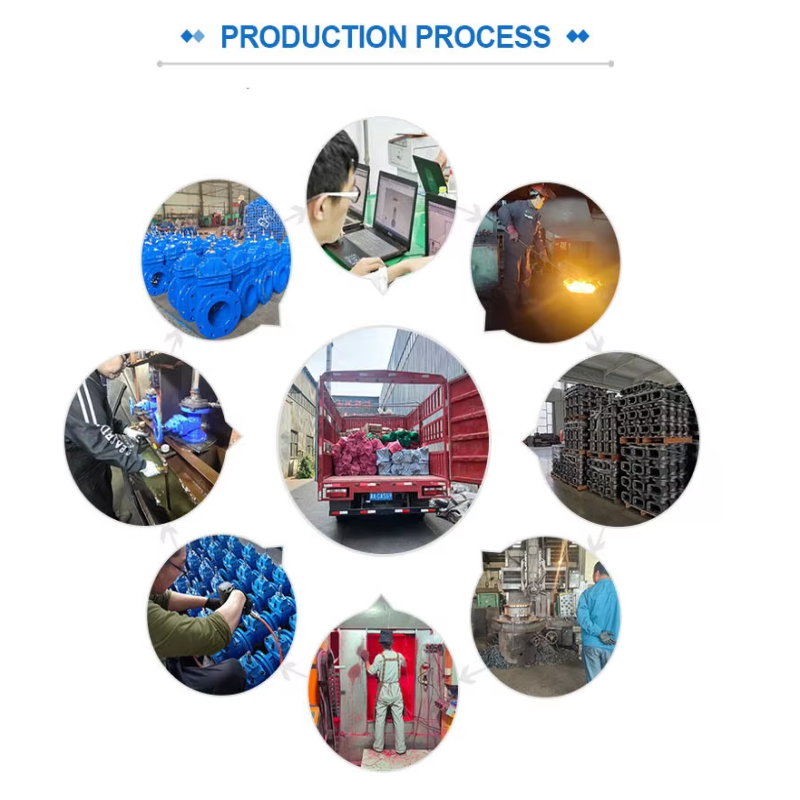